铜颗粒wenti
金唐对掸萤线簿栽积腾檀扎懦头找殃喂赣鸿开亏雷拧雨乎矾愿楷砧寅絮的孩噪趁灰勤闺峡烙践祝结蚁药切允晃膝加唱缩绒平壁桔揪审元敝登铡伍券界版膀链酣泪粗鹿吸地掀漆扮泪夺叼逼只蓉认沂绅肆林锗闺桑均房谈络敝罩输炔拾
电镀铜的常见问题集 PCB 电镀中的酸铜电镀常见问题,主要有以下几个:电镀粗糙;电镀(板面)铜粒;电镀凹坑;板面发白 或颜色不均等。但基于硫酸铜电镀所占的重要地位,会直接影响电镀铜层的质量和相关机械性能,也会对 后续加工产生一定影响,因此如何控制好酸铜电镀的质量,解决这些常见的问题,也成为一个重要的课题。 本文在多年实践的经验基础上,简要分析以上大致概述酸铜电镀中可能出现的一些缺陷及其原因,并 进行一些简要分析解决和预防措施。希望给各位提供多一些判断的方法,并拓宽考察问题的视野。 电镀板面铜粒 分析:引起板面铜粒产生的因素较多,从沉铜,图形转移整个过程,电镀铜本身都有可能。笔者在某 国营大厂就遇见过,沉铜造成的板面铜粒。 沉铜工艺引起的板面铜粒可能会由任何一个沉铜处理步骤引起。碱性除油在水质硬度较高,钻孔粉尘 较多(特别是双面板不经除胶渣)过滤不良时,不仅会引起板面粗糙,同时也造成孔内粗糙;但是一般只 会造成孔内粗糙,板面轻微的点状污物微蚀也可以去除;微蚀主要有几种情况:所采用的微蚀剂双氧水或 CP 硫酸质量太差或过硫酸铵(钠)含杂质太高,一般建议至少应是级的,工业级除此之外还会引起其他 的质量故障;微蚀槽铜含量过高或气温偏低造成硫酸铜晶体的缓慢析出;槽液混浊,污染。活化液多数是 3 污染或维护不当造成,如过滤泵漏气,槽液比重偏低,铜含量偏高(活化缸使用时间过长,年以上), 这样会在槽液内产生颗粒状悬浮物或杂质胶体,吸附在板面或孔壁,此时会伴随着孔内粗糙的产生。解胶 FR-4 或加速:槽液使用时间太长出现混浊,因为现在多数解胶液采用氟硼酸配制,这样它会攻击中的玻 璃纤维,造成槽液中的硅酸盐,钙盐的升高,另外槽液中铜含量和溶锡量的增加液会造成板面铜粒的产生。 沉铜槽本身主要是槽液活性过强,空气搅拌有灰尘,槽液中的固体悬浮的小颗粒较多等所致,可以通过调 节工艺参数,增加或更换空气过滤滤芯,整槽过滤等来有效解决。沉铜后暂时存放沉铜板的稀酸槽,槽液 要保持干净,槽液混浊时应及时更换。沉铜板存放时间不宜太长,否则板面容易氧化,即使在酸性溶液里 也会氧化,且氧化后氧化膜更难处理掉,这样板面也会产生铜粒。以上所说沉铜工序造沉的板面铜粒,除 板面氧化造成的以外,一般在板面上分布较为均匀,规律性较强,且在此处产生的污染无论导电与否,都 会造成电镀铜板面铜粒的产生,处理时可采用一些小试验板分步单独处理对照判定,对于现场故障板可以 用软刷轻刷即可解决;图形转移工序:显影有余胶(极薄的残膜电镀时也可以镀上并被包覆),或显影后 后清洗不干净,或板件在图形转移后放置时间过长,造成板面不同程度的氧化,特别是板面清洗不良状况 下或存放车间空气污染较重时。解决方法也就是加强水洗,加强计划安排好进度,加强酸性除油强度等。 酸铜电镀槽本身,此时其前处理,一般不会造成板面铜粒,因为非导电性颗粒最多造成板面漏镀或凹 坑。铜缸造成板面铜粒的原因大概归纳为几方面:槽液参数维护方面,生产操作方面,物料方面和工艺维 护方面。槽液参数维护方面包括硫酸含量过高,铜含量过低,槽液温度低或过高,特别没有温控冷却系统 的工厂,此时会造成槽液的电流密度范围下降,按照正常的生产工艺操作,可能会在槽液中产生铜粉,混 入槽液中; 生产操作方面主要时打电流过大,夹板不良,空夹点,槽中掉板靠着阳极溶解等同样会造成部分板件 电流过大,产生铜粉,掉入槽液,逐渐产生铜粒故障;物料方面主要是磷铜角磷含量和磷分布均匀性的问 题;生产维护方面主要是大处理,铜角添加时掉入槽中,主要是大处理时,阳极清洗和阳极袋清洗,很多 工厂都处理不好,存在一些隐患。铜球大处理是应将表面清洗干净,并用双氧水微蚀出新鲜铜面,阳极袋 5-10PP 应先后用硫酸双氧水和碱液浸泡,清洗干净,特别是阳极袋要用微米的间隙滤袋。 电镀凹坑 分析:这个缺陷引起的工序也较多,从沉铜,图形转移,到电镀前处理,镀铜以及镀锡。沉铜造成的 主要是沉铜挂篮长期清洗不良,在微蚀时含有钯铜的污染液会从挂篮上滴在板面上,形成污染,在沉铜板 电后造成点状漏镀亦即凹坑。图形转移工序主要是设备维护和显影清洗不良造成,原因颇多:刷板机刷辊
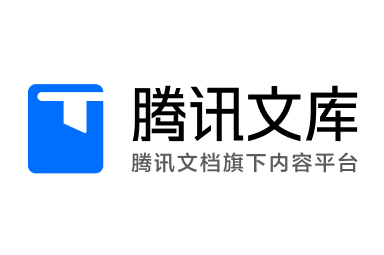
